What is the difference between drone aerial inspection and SolarEdge's optimizer ?
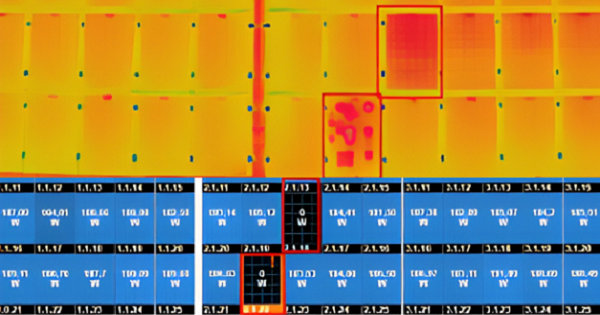
The optimizer offers the advantage of continuously monitoring module power generation during PV plant operation, ensuring efficient performance. In May 2020, SolarEdge published a technical white paper, Power Optimizers Match Infrared (IR) Imaging Capabilities at Finding Module Defects, examining the effectiveness of aerial inspection versus optimizer-based monitoring for solar modules. The study concluded that both methods consistently identify abnormal modules.
Aerial inspection was conducted on a 25KW rooftop PV plant that has been operational for approximately six years and is equipped with the SolarEdge optimizer. Several abnormal modules were identified. The optimizer app indicated that some modules were generating only two-thirds of the power compared to normal modules. Aerial inspection results revealed that one of these modules had a fault classified as "One open circuit in a sub-series within the module," indicative of abnormal diode conduction. Additionally, two other modules showed no power generation in the optimizer app. Aerial inspection results further identified faults: one module exhibited an "open circuit," while the other displayed a "short circuit."
This case demonstrates that both the optimizer and aerial inspection yield consistent results in monitoring modules, while also highlighting their respective strengths and limitations. The optimizer excels in continuous monitoring, immediate anomaly detection, and recording power generation losses. However, it requires additional installation and maintenance costs and cannot directly identify physical failure modes. In contrast, aerial inspection is a cost-effective alternative that avoids optimizer-related failures and provides direct identification of physical faults. Its drawbacks include the complexity of execution, reliance on scheduled inspections to detect anomalies, and the need for professional expertise in fault diagnosis. Additionally, determining the exact time of failure remains a challenge.
This case demonstrates that both the optimizer and aerial inspection yield consistent results in monitoring modules, while also highlighting their respective strengths and limitations. The optimizer excels in continuous monitoring, immediate anomaly detection, and recording power generation losses. However, it requires additional installation and maintenance costs and cannot directly identify physical failure modes. In contrast, aerial inspection is a cost-effective alternative that avoids optimizer-related failures and provides direct identification of physical faults. Its drawbacks include the complexity of execution, reliance on scheduled inspections to detect anomalies, and the need for professional expertise in fault diagnosis. Additionally, determining the exact time of failure remains a challenge.